Could new mortar reduce heat losses?
- Specify & Build
- 3 days ago
- 2 min read
An environmentally-friendly mortar made from recycled plastic and silica aerogel has been developed by Newcastle University researchers to improve insulation and reduce plastic waste.
The cement mortar mix was developed by replacing sand with silica aerogel and recycled PET plastic, which showed improved thermal insulation and weighs less. Aerogels are known for their high insulation properties and are increasingly used for thermal insulation, particularly within the building sector and aerospace sectors. Testing showed that the new mortar mix reduced heat loss by up to 55% compared to conventional mortar, the University said, while maintaining the required strength for masonry construction.
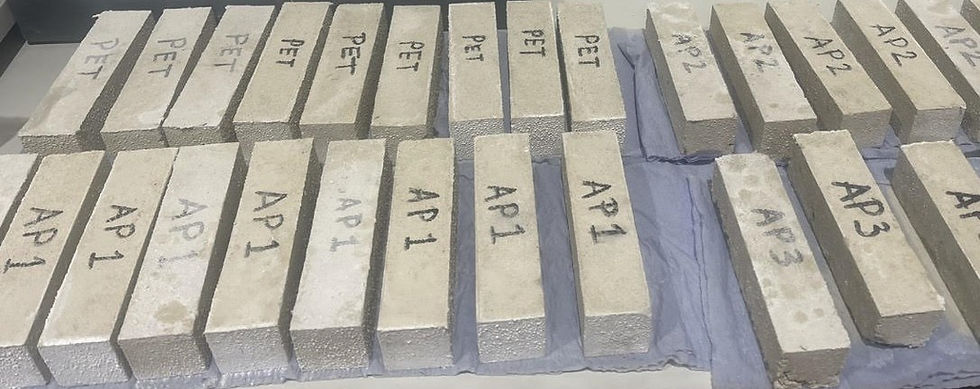
It also meets international standards (BS-EN 413-1:2011, ASTM C270-10, AS 1012/AS 3700), presenting an eco-friendly alternative for energy-efficient and sustainable construction. The team believes this could improve sustainable construction practices while reducing heat loss in buildings in areas where you get thermal bridging, for example through gaps between bricks in the walls which are filled with mortar.
Professor Lidija Šiller, Professor of Nanoscale Science at Newcastle University’s School of Engineering and one of the study’s lead authors, said: “This study demonstrates that our formulation of recycled PET plastic waste can be used to produce cement-based mortars, and it is an effective way to reduce their impact on the environment. Wouldn’t be wonderful to reduce heating bills in our newbuilds and at the same time significantly reduce plastic waste in the world?’’

The new mortar mix
Seven different formulations were tested alongside traditional mortar with the most effective of the new mortar mixes proving to be 7% untreated silica aerogels replacing natural sand combined with 3% recycled PET (polyethene terephthalate) plastic.
The PET plastic particles used in the study came from shredded plastic bottles waste and were coarse, irregular in shape and between 2.5-3.5 mm. The scientists washed the plastic pieces with water after shredding and left them to dry at room temperature for 24 hours.
The team analysed key properties, such as setting time, flowability (a measure to determine the workability of cement mortar), density, strength, and thermal conductivity. The new formulation helped reduce the thermal conductivity of mortar by up to 55%, compared to standard mortar samples.
The scientists are now looking for partners to help them test the new mix in large-scale, real-world setting.